PP plastic pails, also known as buckets, are widely used in various industries for their durability, versatility, and cost-effectiveness. The process of PP plastic pail moulding plays a crucial role in creating these sturdy and functional containers.
The first step in PP plastic pail moulding is the design and prototyping phase. Skilled designers use computer-aided design (CAD) software to create a 3D model of the pail, taking into account its dimensions, capacity, and desired features. This stage allows for adjustments and improvements to the design before moving forward with the moulding process.
Polypropylene (PP) is the primary material used in the production of plastic pails. PP offers excellent durability, chemical resistance, and impact strength, making it ideal for various industrial applications. The selection of high-quality PP resin is crucial to ensure the final product's strength and longevity.
Once the design is finalized and the raw materials are chosen, the mould for the plastic pail is fabricated. Moulds are typically made from hardened steel or aluminum, depending on the desired production volume and cost considerations. Skilled toolmakers use precision machinery and techniques to create moulds that accurately reflect the pail's design.
Injection moulding is the main process used to manufacture PP plastic pails. It involves injecting molten PP resin into the mould cavity under high pressure and temperature. The resin is melted in an extruder and then injected into the mould, where it takes the shape of the pail. The high pressure ensures that the resin fills every detail of the mould, resulting in a precise and uniform product.
After the molten resin is injected into the mould, it undergoes a cooling and solidification process. The mould is typically equipped with cooling channels to facilitate rapid and controlled cooling. Cooling time varies depending on the pail's size and thickness. Once the plastic has solidified, the mould is opened, and the newly formed plastic pail is ejected.
The ejected plastic pails may have excess material, called flash, which needs to be removed. Trimming processes, such as mechanical or laser cutting, are employed to remove the flash and achieve the desired shape and smoothness of the pail's edges. Additional finishing processes, such as printing or labeling, may be performed to add branding or product information.
To ensure the highest standards of quality, the manufactured plastic pails undergo rigorous inspection. This involves checking for dimensional accuracy, strength, and overall integrity of the pails. Various tests may be conducted, including leak tests, impact tests, and stress tests, to assess the performance and durability of the pails.
PP plastic pail moulding is a precise and efficient manufacturing process that produces durable and versatile containers. From design and raw material selection to mould fabrication and injection moulding, each step in the process is crucial to creating high-quality plastic pails. With their durability, chemical resistance, and impact strength, PP plastic pails find applications in industries ranging from food and beverage to agriculture and construction. Understanding the process of PP plastic pail moulding highlights the craftsmanship and attention to detail involved in creating these reliable and functional containers.
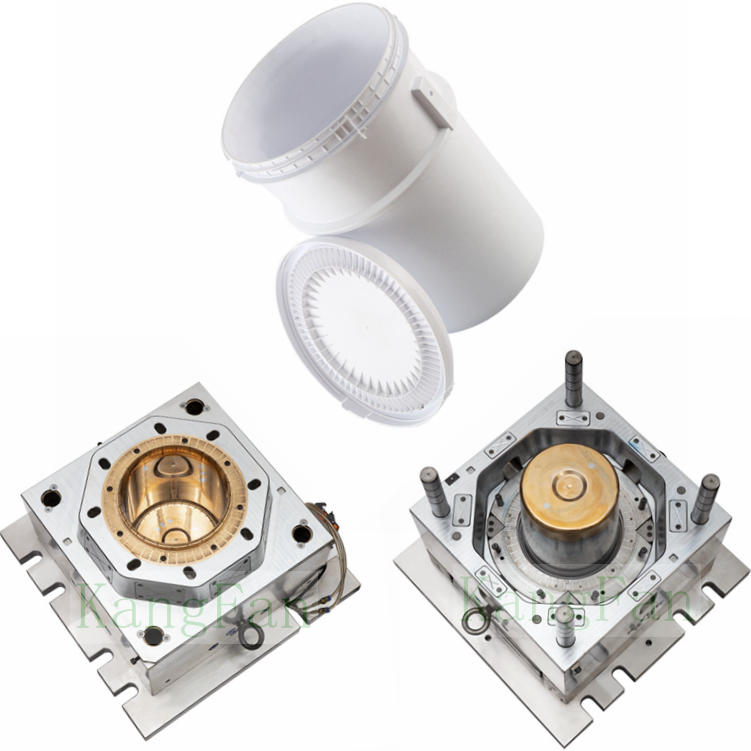
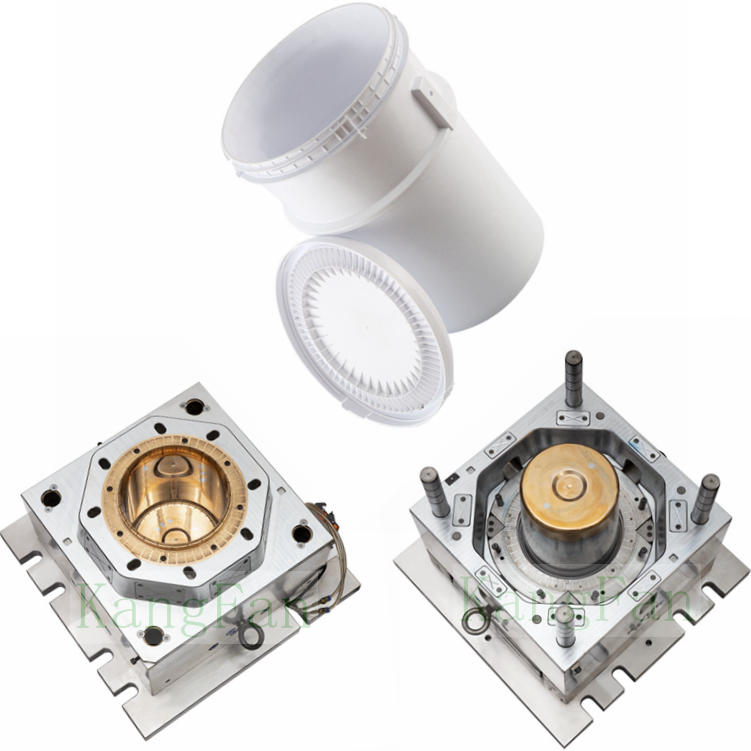